Produción de tecidos non tecidos por fundición de polipropileno
Fundir o tecido non tecido
Visión xeral
Diferentes usos ou niveis de máscaras de protección e roupa utilizan diferentes materiais e métodos de preparación, xa que o maior nivel de máscaras de protección médica (como N95) e roupa de protección, de tres a cinco capas de composto de tecido non tecido, a saber, combinación SMS ou SMMMS.
A parte máis importante destes equipos de protección é a capa de barreira, é dicir, a capa M non tecida que non se desgarra, o diámetro da fibra da capa é relativamente fino, 2 ~ 3μm, xoga un papel vital na prevención da infiltración de bacterias e sangue. O pano de microfibra mostra un bo filtro, permeabilidade ao aire e adsorbabilidade, polo que se usa amplamente en materiais de filtración, materiais térmicos, hixiene médica e outros campos.
Melt de polipropileno Blow Blow non tecido Tecnoloxía e proceso de produción de tecidos
O proceso de produción de tecido non tecido de fusión é xeralmente alimentación de porcións de resina de polímero → Extrusión de fusión → Filtración de impureza de fusión → Bomba de medición Medición precisa → Spinet → Malla → Enrolamento de bordo → Procesamento de produtos.
O principio do proceso de soplado de fusión é extruir o polímero fundido do burato spinneret da cabeza para formar un fino fluxo de derretimento. Ao mesmo tempo, o fluxo de aire de alta velocidade e alta temperatura a ambos os dous lados dos sprays de buraco de espinet e estira o fluxo de fusión, que logo se perfecciona en filamentos cunha finura de só 1 ~ 5μm. Estes filamentos son entón tirados a fibras curtas de aproximadamente 45 mm polo fluxo térmico.
Para evitar que o aire quente soprase a fibra curta, establécese un dispositivo de succión de baleiro (baixo a pantalla de coagulación) para recoller uniformemente a microfibra formada por estiramento de aire quente de alta velocidade. Finalmente, confía nun autoadhesivo para facer tecido non tecido.
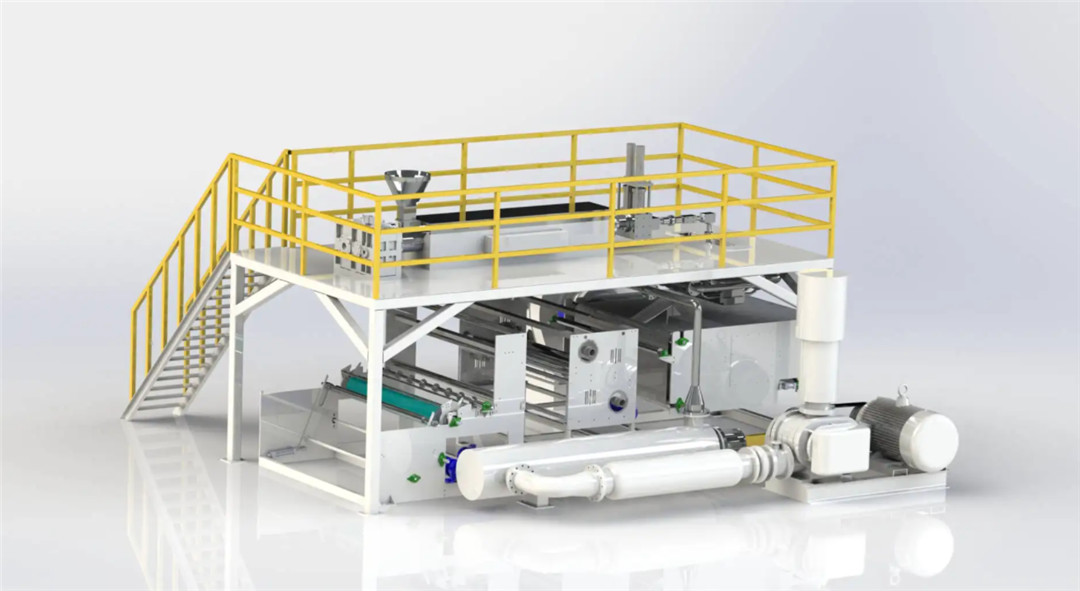
Parámetros principais do proceso:
Propiedades das materias primas de polímeros: incluíndo propiedades reolóxicas das materias primas de resina, contido de cinzas, distribución de masa molecular relativa, etc. Entre elas, as propiedades reolóxicas das materias primas é o índice máis importante, expresado comunmente por índice de fusión (IMF). Canto maior sexa a IMF, mellor será a fluidez fundida do material e viceversa. Canto menor sexa o peso molecular do material de resina, maior será a IMF e a menor é a viscosidade do fundido, máis adecuada para o proceso de explosión de fusión con malos elementos. Para o polipropileno, a IMF debe estar no rango de 400 ~ 1800g / 10min.
No proceso de produción de explosións de fusión, os parámetros axustados segundo a demanda de materias primas e produtos inclúen principalmente:
(1) Cantidade de extrusión de fusión Cando a temperatura é constante, a cantidade de extrusión aumenta, a cantidade non tecida soplada aumenta e a forza aumenta (diminúe despois de alcanzar o valor máximo). A súa relación co diámetro da fibra aumenta linealmente, a cantidade de extrusión é demasiado, o diámetro da fibra aumenta, o número de raíz diminúe e a forza diminúe, a parte de unión diminúe, causando e seda, polo que a forza relativa do pano non tecido diminúe.
(2) A temperatura de cada área do parafuso non só está relacionada coa suavidade do proceso de fiación, senón que tamén afecta o aspecto, a sensación e o rendemento do produto. A temperatura é demasiado alta, haberá polímero de bloque "disparado", aumentan os defectos do pano, o aumento da fibra rota, aparecen "voando". A configuración de temperatura inadecuada pode causar bloqueo da cabeza de aspersión, desgastar o burato de spinneret e danar o dispositivo.
(3) A temperatura do aire quente estiramento da temperatura do aire quente exprésase xeralmente pola velocidade do aire quente (presión), ten un impacto directo na finura da fibra. No caso doutros parámetros son os mesmos, aumentan a velocidade do aire quente, o adelgazamento da fibra, o nodo de fibra aumenta, a forza uniforme, a forza aumenta, a sensación non tecida faise suave e suave. Pero a velocidade é demasiado grande, fácil de aparecer "voando", afecta a aparencia de tecido non tecido; Coa diminución da velocidade, a porosidade aumenta, a resistencia á filtración diminúe, pero a eficiencia de filtración deteriora. Cómpre salientar que a temperatura do aire quente debe estar preto da temperatura de fusión, se non, xerarase o fluxo de aire e a caixa será danada.
(4) A temperatura de fusión da temperatura de fusión, tamén coñecida como a temperatura da cabeza de fusión, está estreitamente relacionada coa fluidez do fundido. Co aumento da temperatura, a fluidez fundida faise mellor, a viscosidade diminúe, a fibra faise máis fina e a uniformidade faise mellor. Non obstante, canto máis baixa sexa a viscosidade, a mellor viscosidade, demasiado baixa, provocará unha redacción excesiva, a fibra é fácil de romper, non se pode recoller a formación de microfibra ultra-curta no aire.
(5) A distancia de recepción da distancia de recepción (DCD) refírese á distancia entre a spinneret e a cortina de malla. Este parámetro ten unha influencia especialmente significativa na forza da malla de fibra. Co aumento da DCD, diminúe a resistencia e a rixidez da flexión, o diámetro da fibra diminúe e o punto de unión diminúe. Polo tanto, o tecido non tecido é suave e esponjoso, aumenta a permeabilidade e a resistencia á filtración e a eficiencia de filtración diminúen. Cando a distancia é demasiado grande, o borrador da fibra redúcese polo fluxo de aire quente e o enredamento producirase entre as fibras no proceso de redacción, dando lugar a filamentos. Cando a distancia de recepción é demasiado pequena, a fibra non se pode arrefriar completamente, dando lugar a unha forza de tecido non tecida, diminúe, aumenta a incapacidade.