2022 China New Design Weed Stop Membrane - Polypropylene melt blown non – woven fabric production – Medlong
2022 China New Design Weed Stop Membrane - Polypropylene melt blown non – woven fabric production – Medlong Detail:
Melt blown nonwoven fabric
Overview
Different uses or levels of protective masks and clothing use different materials and preparation methods, as the highest level of medical protective masks (such as N95) and protective clothing, three to five layers of non-woven fabric composite, namely SMS or SMMMS combination.
The most important part of these protective equipment is the barrier layer, namely melt-blown non-woven layer M, the fiber diameter of the layer is relatively fine, 2 ~ 3μm, it plays a vital role in preventing the infiltration of bacteria and blood. The microfiber cloth shows good filter, air permeability and adsorbability, so it is widely used in filtration materials, thermal materials, medical hygiene and other fields.
Polypropylene melt blown non – woven fabric production technology and process
Melt blown non-woven fabric production process is generally polymer resin slice feeding → melt extrusion → melt impurity filtration → metering pump accurate metering → spinet → mesh → edge winding → product processing.
The principle of melt blowing process is to extrude polymer melt from the spinneret hole of the die head to form a thin flow of melt. At the same time, the high-speed and high-temperature air flow on both sides of the spinet hole sprays and stretches the melt stream, which is then refined into filaments with a fineness of only 1 ~ 5μm. These filaments are then pulled to short fibers of about 45mm by the thermal flow.
In order to prevent the hot air from blowing the short fiber apart, a vacuum suction device is set (under the coagulation screen) to evenly collect the microfiber formed by high-speed hot air stretching. Finally, it relies on self-adhesive to make melt-blown nonwoven fabric.
Main process parameters:
Properties of polymer raw materials: including rheological properties of resin raw materials, ash content, relative molecular mass distribution, etc. Among them, rheological properties of raw materials is the most important index, commonly expressed by melting index (MFI). The greater the MFI, the better the melt fluidity of the material, and vice versa. The lower the molecular weight of the resin material, the higher the MFI and the lower the melt viscosity, the more suitable for the melt blowout process with poor drafting. For polypropylene, the MFI is required to be in the range of 400 ~ 1800g / 10mIN.
In the process of melt blowout production, the parameters adjusted according to the demand of raw materials and products mainly include:
(1) Melt extrusion quantity when the temperature is constant, the extrusion quantity increases, the melt blown nonwoven quantity increases, and the strength increases (decreases after reaching the peak value). Its relationship with the fiber diameter linearly increases, the amount of extrusion is too much, the fiber diameter increases, the root number decreases and the strength decreases, the bonding part decreases, causing and silk, so the relative strength of non-woven cloth decreases.
(2) the temperature of each area of the screw is not only related to the smoothness of the spinning process, but also affects the appearance, feel and performance of the product. The temperature is too high, there will be “SHOT” block polymer, cloth defects increase, broken fiber increase, appear “flying”. Improper temperature Settings may cause blockage of the sprinkler head, wear out the spinneret hole, and damage the device.
(3) Stretch hot air temperature Stretch hot air temperature is generally expressed by hot air velocity (pressure), has a direct impact on the fineness of the fiber. In the case of other parameters are the same, increase the speed of hot air, fiber thinning, fiber node increases, uniform force, strength increases, non-woven feel becomes soft and smooth. But the speed is too large, easy to appear “flying”, affect the appearance of non-woven fabric; With the decrease of velocity, the porosity increases, the filtration resistance decreases, but the filtration efficiency deteriorates. It should be noted that the hot air temperature should be close to the melt temperature, otherwise airflow will be generated and the box will be damaged.
(4) Melt temperature Melt temperature, also known as melt head temperature, is closely related to melt fluidity. With the increase of temperature, the melt fluidity becomes better, the viscosity decreases, the fiber becomes finer and the uniformity becomes better. However, the lower the viscosity, the better, too low viscosity, will cause excessive drafting, fiber is easy to break, the formation of ultra-short microfiber flying in the air can not be collected.
(5) Receiving distance Receiving distance (DCD) refers to the distance between the spinneret and the mesh curtain. This parameter has a particularly significant influence on the strength of the fiber mesh. With the increase of DCD, the strength and bending stiffness decrease, the fiber diameter decreases, and the bonding point decreases. Therefore, the non-woven fabric is soft and fluffy, the permeability increases, and the filtration resistance and filtration efficiency decrease. When the distance is too large, the draft of the fiber is reduced by the hot air flow, and the entanglement will occur between the fibers in the process of drafting, resulting in filaments. When the receiving distance is too small, the fiber can not be completely cooled, resulting in wire, non-woven fabric strength decreases, brittleness increases.
Product detail pictures:
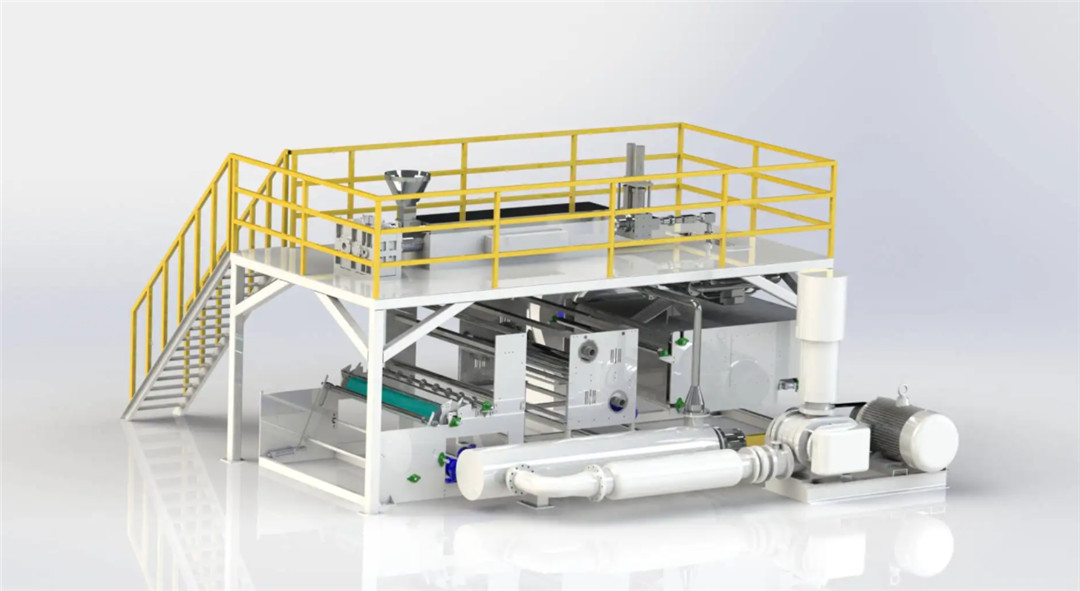
Related Product Guide:
Dedicated to strict quality control and thoughtful customer service, our experienced staff members are always available to discuss your requirements and ensure full customer satisfaction for 2022 China New Design Weed Stop Membrane - Polypropylene melt blown non – woven fabric production – Medlong, The product will supply to all over the world, such as: Danish , Guyana , Panama , For anyone who is keen on any of our items right after you view our product list, you should definitely feel absolutely free to get in touch with us for inquiries. You are able to send us emails and contact us for consultation and we shall respond to you as soon as we can. If it's easy, you may locate out our address in our web-site and come to our business for far more information of our merchandise by your self. We're always ready to construct extended and steady co-operation relations with any possible customers in the related fields.

The customer service staff's attitude is very sincere and the reply is timely and very detailed, this is very helpful for our deal,thank you.
