Producción de tela no tejida fundida por soplado de polipropileno
Tela no tejida fundida por soplado
Descripción general
Los diferentes usos o niveles de mascarillas y ropa protectora utilizan diferentes materiales y métodos de preparación, ya que el nivel más alto de mascarillas protectoras médicas (como N95) y ropa protectora, de tres a cinco capas de tejido no tejido compuesto, es decir, combinación SMS o SMMMS.
El componente más importante de estos equipos de protección es la capa de barrera, concretamente la capa M de tejido no tejido fundido por soplado. El diámetro de la fibra es relativamente fino (2-3 μm), lo que desempeña un papel fundamental en la prevención de la infiltración de bacterias y sangre. La tela de microfibra presenta una buena capacidad de filtración, permeabilidad al aire y adsorción, por lo que se utiliza ampliamente en materiales de filtración, materiales térmicos, higiene médica y otros campos.
Tecnología y proceso de producción de tela no tejida fundida por soplado de polipropileno
El proceso de producción de tela no tejida fundida por soplado generalmente consiste en alimentación de rodajas de resina polimérica → extrusión de la masa fundida → filtración de impurezas de la masa fundida → dosificación precisa con bomba dosificadora → espineta → malla → bobinado de bordes → procesamiento del producto.
El principio del proceso de soplado por fusión consiste en extruir polímero fundido desde el orificio de la hilera del cabezal de la matriz para formar un flujo fino de material fundido. Simultáneamente, el flujo de aire a alta velocidad y temperatura a ambos lados de la hilera pulveriza y estira el flujo de material fundido, que posteriormente se refina en filamentos con una finura de tan solo 1 ~ 5 μm. Estos filamentos se estiran hasta formar fibras cortas de aproximadamente 45 mm mediante el flujo térmico.
Para evitar que el aire caliente separe las fibras cortas, se instala un dispositivo de succión al vacío (debajo de la pantalla de coagulación) para recolectar uniformemente la microfibra formada mediante el estiramiento con aire caliente a alta velocidad. Finalmente, se utiliza autoadhesivo para fabricar tela no tejida fundida por soplado.
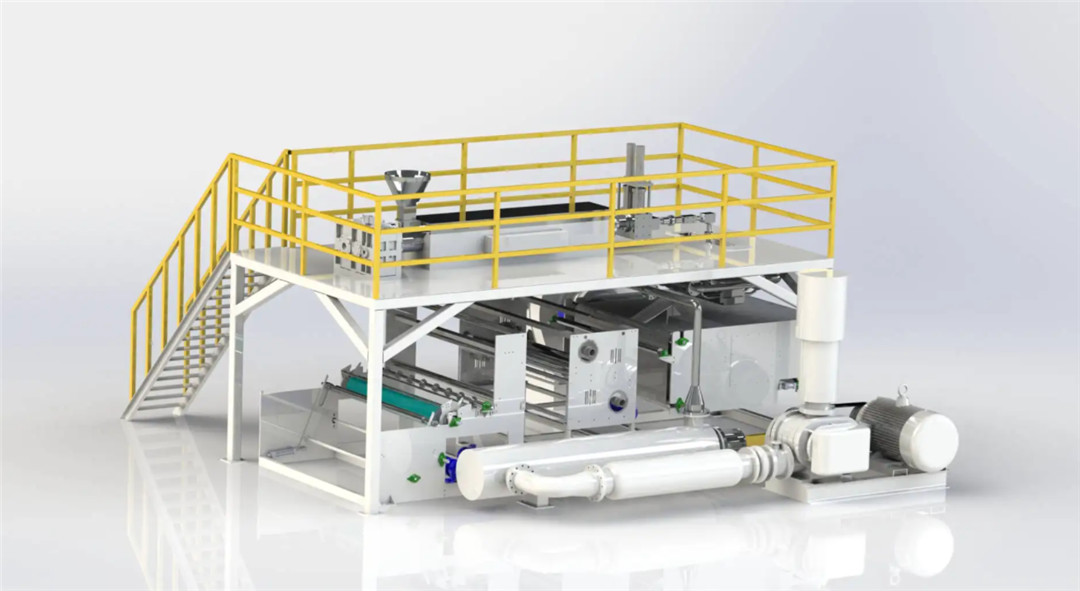
Parámetros principales del proceso:
Propiedades de las materias primas poliméricas: incluye las propiedades reológicas de las resinas, el contenido de cenizas, la distribución relativa de la masa molecular, etc. Entre ellas, las propiedades reológicas de las materias primas son el índice más importante, comúnmente expresado por el índice de fusión (MFI). Cuanto mayor sea el MFI, mejor será la fluidez del material en estado fundido, y viceversa. Cuanto menor sea el peso molecular de la resina, mayor será el MFI y menor la viscosidad del material en estado fundido, lo que la hace más adecuada para el proceso de soplado en estado fundido con un estirado deficiente. Para el polipropileno, el MFI debe estar entre 400 y 1800 g/10 min.
En el proceso de producción de soplado de masa fundida, los parámetros ajustados según la demanda de materias primas y productos incluyen principalmente:
(1) A temperatura constante, la cantidad de extrusión por fusión aumenta, la cantidad de no tejido fundido por soplado aumenta y la resistencia aumenta (disminuye tras alcanzar el valor máximo). Su relación con el diámetro de la fibra aumenta linealmente. Si la cantidad de extrusión es excesiva, el diámetro de la fibra aumenta, el número de raíces disminuye y la resistencia disminuye. La parte de unión disminuye, lo que provoca sedosidad, por lo que la resistencia relativa de la tela no tejida disminuye.
(2) La temperatura de cada área del tornillo no solo influye en la suavidad del hilado, sino que también afecta la apariencia, la sensación y el rendimiento del producto. Una temperatura demasiado alta puede producir "desplazamientos" del polímero en bloque, aumentar los defectos de la tela y la rotura de fibras, y aparecer "desplazamientos". Un ajuste incorrecto de la temperatura puede obstruir el cabezal del rociador, desgastar el orificio de la hilera y dañar el dispositivo.
(3) Temperatura del aire caliente de estiramiento. La temperatura del aire caliente de estiramiento se expresa generalmente por la velocidad (presión) del aire caliente y tiene un impacto directo en la finura de la fibra. En el caso de que otros parámetros sean iguales, al aumentar la velocidad del aire caliente, la fibra se adelgaza, el nudo de la fibra aumenta, la fuerza uniforme y la resistencia aumentan, y la tela no tejida se siente suave y lisa. Sin embargo, una velocidad demasiado alta puede provocar que la tela no tejida parezca "volada", lo que afecta la apariencia de la tela. Al disminuir la velocidad, la porosidad aumenta, la resistencia a la filtración disminuye y la eficiencia de filtración se deteriora. Es importante tener en cuenta que la temperatura del aire caliente debe ser cercana a la temperatura de fusión; de lo contrario, se generará un flujo de aire que dañará la caja.
(4) Temperatura de fusión. La temperatura de fusión, también conocida como temperatura del cabezal de fusión, está estrechamente relacionada con la fluidez de la fusión. Al aumentar la temperatura, la fluidez de la fusión mejora, la viscosidad disminuye, la fibra se vuelve más fina y la uniformidad mejora. Sin embargo, cuanto menor sea la viscosidad, mejor. Una viscosidad demasiado baja provocará un estirado excesivo, la fibra se romperá con facilidad y las microfibras ultracortas que salen volando por el aire no se podrán recoger.
(5) Distancia de recepción La distancia de recepción (DCD) se refiere a la distancia entre la hilera y la cortina de malla. Este parámetro tiene una influencia particularmente significativa en la resistencia de la malla de fibra. Con el aumento de la DCD, la resistencia y la rigidez a la flexión disminuyen, el diámetro de la fibra disminuye y el punto de unión disminuye. Por lo tanto, la tela no tejida es suave y esponjosa, la permeabilidad aumenta y la resistencia y la eficiencia de filtración disminuyen. Cuando la distancia es demasiado grande, el tiro de la fibra se reduce por el flujo de aire caliente y el enredo se producirá entre las fibras en el proceso de tiro, lo que resulta en filamentos. Cuando la distancia de recepción es demasiado pequeña, la fibra no se puede enfriar completamente, lo que resulta en alambre, la resistencia de la tela no tejida disminuye y la fragilidad aumenta.